Influence of Rotational Speed on Subsurface Microstructure and Wear Property of D2/U71Mn Wheel-Rail Steel
Chunpeng Liua , Guanzhen Zhangb,c , Chuanwei Lia , Jianfeng Gua , and Ruiming Renb
a Shanghai Key Laboratory of Materials Laser Processing and Modification, School of Materials Science and Engineering, Shanghai Jiaotong University, Shanghai 200240, P. R. China;
b School of Material Science and Engineering, Dalian Jiaotong University, Dalian 116028, P. R. China;
c Metals and Chemistry Research Institute, China Academy of Railway Sciences Corporation Limited, Beijing, 100081, P. R. China
Abstract
In this article, the effect of rotational speed on the subsurface microstructure and wear property of D2/U71Mn wheel–rail steel is studied under pure rolling conditions. Rolling wear experiments were conducted using a GPM-40 rolling wear tester. The subsurface microstructure and surface morphology of the wheel and rail samples under different rotational speed conditions were analyzed using an optical microscope and field emission scanning electron microscopy. The results showed that the rotational speed significantly influences the wear property of the wheel materials. A low rotational speed could increase the friction stress at the wheel–rail contact surface, and the weight loss of the wheel sample was large under low rotational speeds. As the rotational speed increased, the weight loss of the wheel sample decreased gradually, but the change in the weight loss of the rail sample was not obvious. The thickness of the plastic deformation layer of the wheel sample increased as the rotational speed increased. However, the variation of the plastic deformation layer of the rail sample was not obvious. During the rolling wear process, a gradient plastic deformation layer (the surface was a severe plastic deformation layer, and the subsurface was a plastic flow layer) was formed at the wheel–rail sample surface. In the severe plastic deformation layer, ferrite grains were refined obviously, and lamellar cementite was fragmented into cementite particles. In the plastic flow layer, the ferrite grains produced obvious plastic deformation, but the change in the lamellar cementite was not obvious. During the rolling wear process, the relationship between wear and fatigue was competitive. Under low rotational speed conditions, the high weight loss of the wheel sample could inhibit the formation of fatigue cracks. As the rotational speed increased, the weight loss of the wheel sample decreased gradually, and the length of the fatigue cracks increased. The wear mechanism of the wheel sample transformed into fatigue wear. However, the surface worn morphology of the rail sample had no significant change under 600-r/min and 1000-r/min conditions. The length of fatigue cracks of the rail sample is slightly reduced under the 1440-r/min condition due to the increase of a small amount of weight loss.
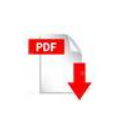
|